Introduction
The global movement toward reducing or banning plastics has gained significant traction. China implemented its first plastic restriction policy in December 2007, limiting the production, sale, and usage of plastic products. Today, over 30 countries and regions worldwide have enacted legislation to control or prohibit plastic in various industries, intensifying efforts year after year.
Pulp molding, made from annual plant fibers through compression molding, has emerged as a popular alternative under these plastic-reduction initiatives. This eco-friendly technology offers the packaging industry a transformative opportunity to adapt to changing environmental policies and market demands.

Understanding Pulp Molding: Definitions, Features, and Classifications
1. Definition of Pulp Molding
- Broad Definition: Pulp molding refers to a manufacturing process that uses raw materials such as pulp or straw fibers. Through processes such as pulping, injection (or suction, scooping), molding, shaping, trimming, inspection, sterilization, and packaging, various 3D products like industrial packaging, tableware, agricultural containers, masks, and decorative wall panels are created. It is a form of 3D papermaking.
- Narrow Definition: It refers to using recycled paper pulp, such as yellow pulp or newspaper pulp, to produce low-end, simple 3D products like industrial liners and egg trays.
2. Features of Pulp Molding
- Uses renewable resources like wheat, bamboo, sugarcane, palm, and reed fibers, reducing reliance on forest wood.
- Zero wastewater discharge during production.
- Products are oil- and water-resistant.
- Suitable for freezing, refrigeration, microwave heating, and baking at 220°C.
- Biodegrades within 45-90 days and can be composted at home, leaving no residual pollutants.
- Provides cushioning, compression resistance, and shock absorption, ideal for protective packaging.
- Anti-static properties make it suitable for electronic packaging.
3. Classifications of Pulp Molding
- By Process: Wet press, dry press, and hybrid methods.
- By Application: Premium packaging (e.g., electronics), standard packaging (e.g., egg trays), food packaging, agricultural packaging (e.g., seedling pots), medical packaging, construction materials, and entertainment products (e.g., masks).
- By Material: Sugarcane pulp, wheat straw pulp, bamboo pulp, recycled paper pulp, and more.
- By Color: Natural (unbleached) and white.
- By Functional Coatings: Products with or without coatings, such as PE, PLA, or PBAT.
- By Printing: Color-printed, non-printed, and dyed products.
- By Molding Technique: Injection, suction, and scooping methods.
- By Surface Texture: Smooth or textured finishes.
- By Automation: Manual, semi-automatic, and fully automated.
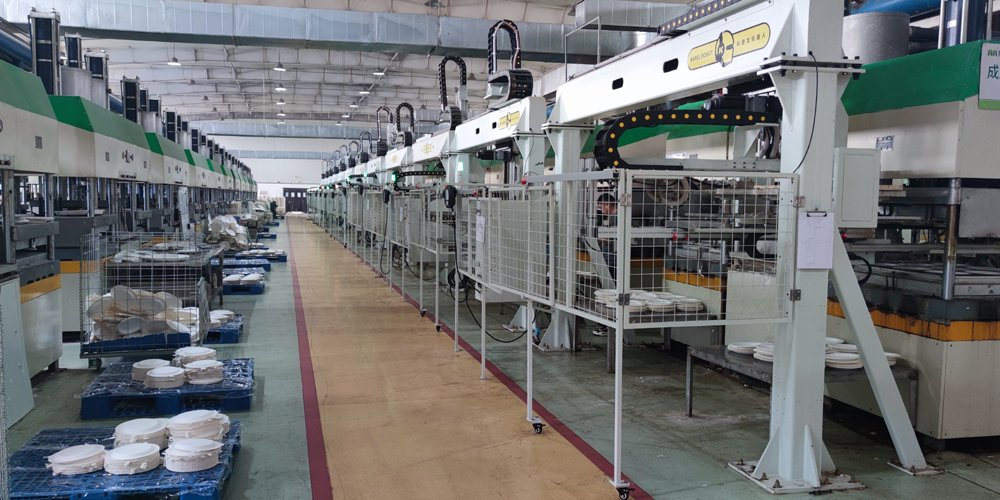
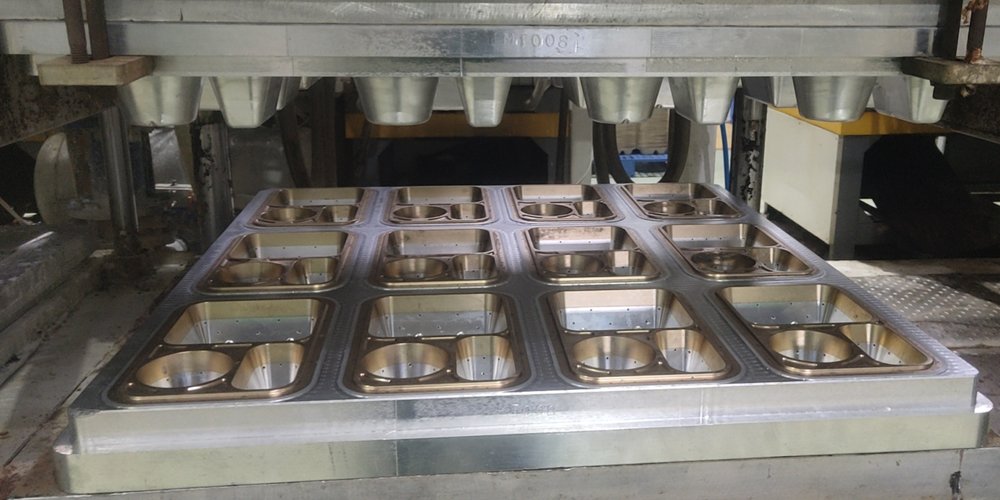
Market Prospects and Development Trends
1. Food Packaging as a Foundation
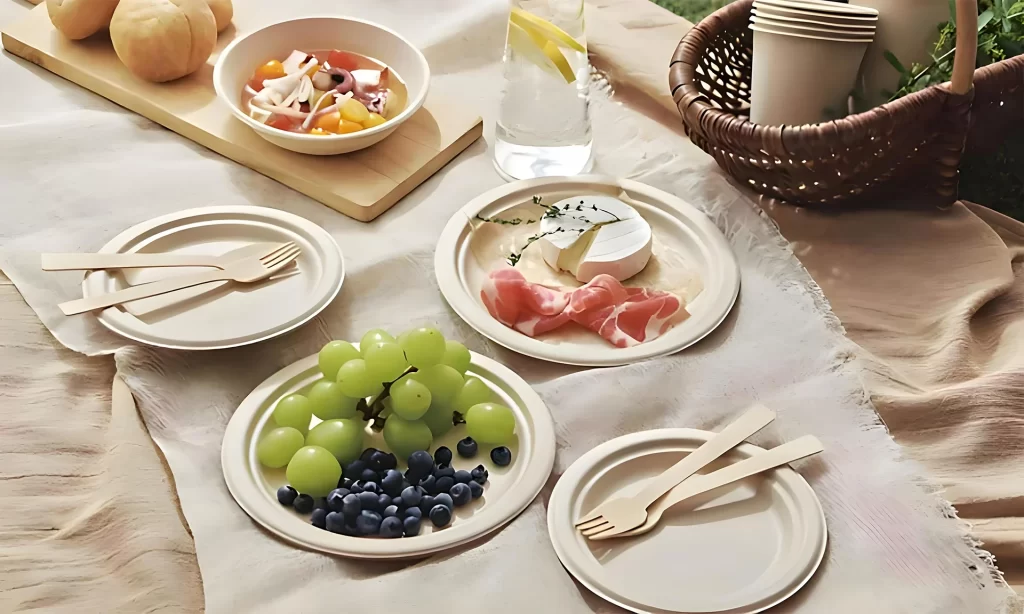

- Tableware: Pulp molded tableware has applications in restaurants, entertainment venues, and conferences, with global demand projected to surpass 250 billion units by 2025.
- Baking Packaging: Straw fiber cake trays and bases have grown in popularity due to their strength and versatility, aligning with trends in high-end bakery goods.
2. Industrial Packaging


- Brands like Dell and Apple are replacing traditional foam with molded pulp for electronics packaging. This shift is driven by international regulations to reduce white pollution, creating significant demand.
3. Medical Packaging
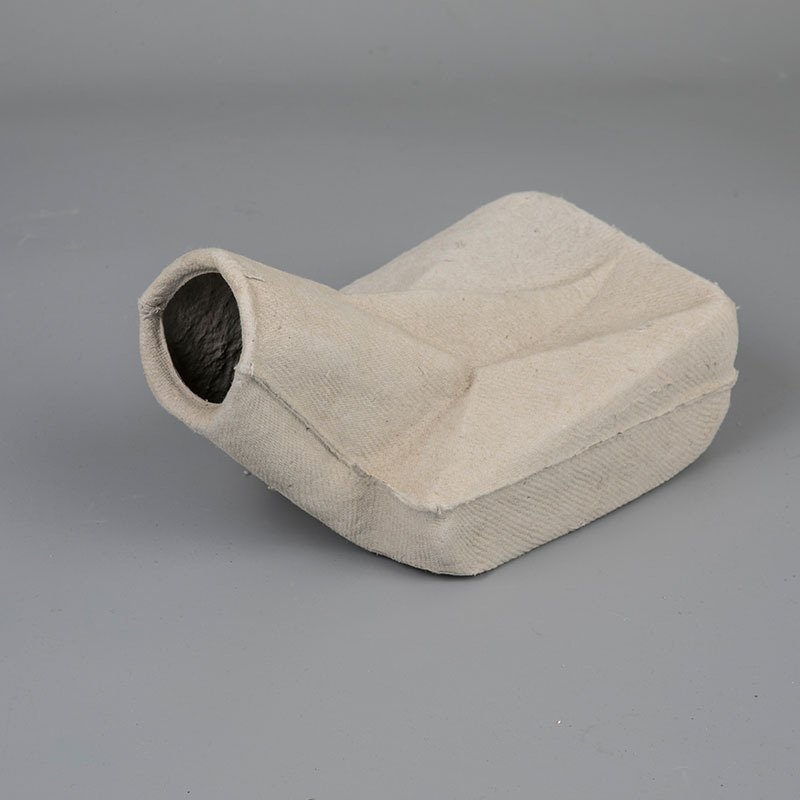

- Products like pulp-based bedpans and urinals are hygienic, disposable, and reduce cross-contamination. With increasing investments in healthcare, demand for single-use medical supplies is expected to grow.
4. Agricultural Packaging
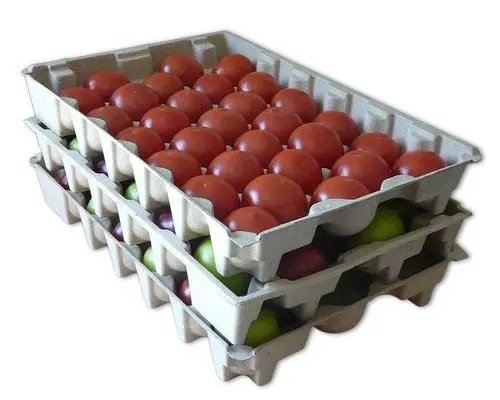

- Egg trays, seedling pots, and fruit containers are widely used and environmentally friendly, supported by policies promoting sustainable agriculture.
5. Emerging Applications
- Entertainment toys and masks: Particularly popular for events in Western markets.
- Construction materials: Including decorative wall panels and insulation boards.
Current Challenges in the Industry
1. Supply-Demand Imbalance


Rising demand for pulp molded products, especially in tableware, has outpaced production capacity, creating supply shortages.
2. Labor-Intensive Processes
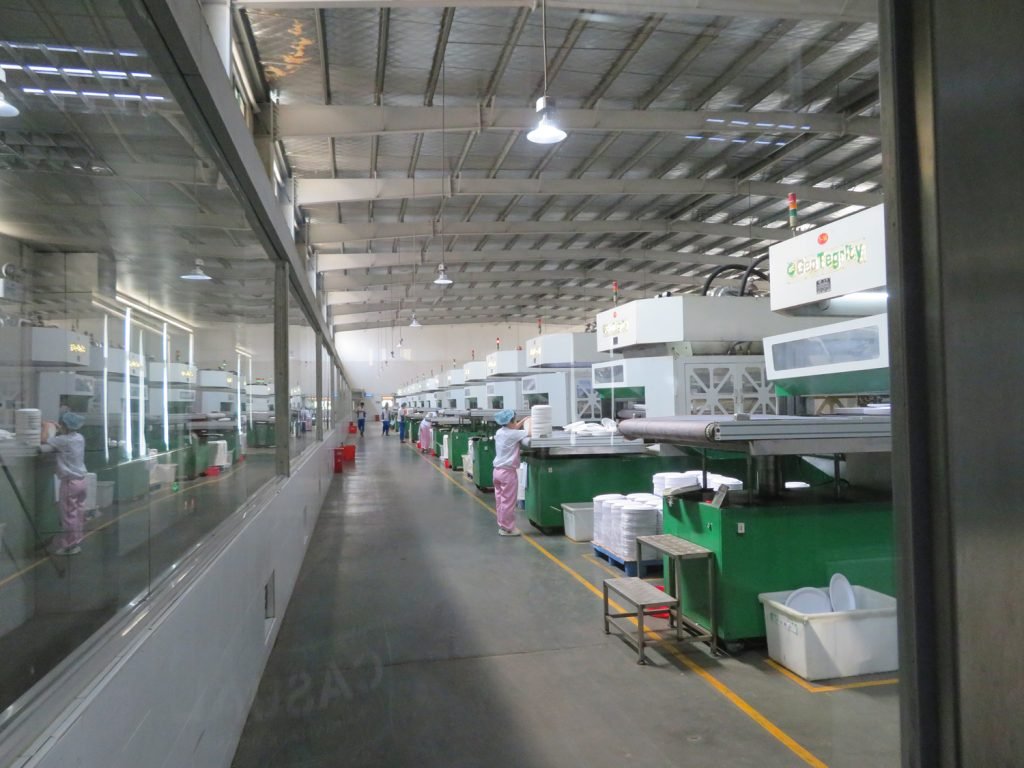
The industry’s reliance on manual labor limits scalability and increases costs, particularly in regions with higher labor expenses.
3. High Energy Consumption
Heat and electricity costs account for 20-25% of total production costs, reducing price competitiveness.
4. Lack of Research and Development
Slow technological progress and outdated machinery hinder industry growth. Increased R&D investment is essential for long-term advancement.
5. Talent Shortages
A lack of skilled professionals has limited innovation and competitiveness. Developing a talent pipeline is critical to addressing this issue.
6. Lack of Industrial Clusters
Fragmented operations and lack of collaboration among manufacturers result in inefficiencies and higher costs. Creating industry clusters could enhance scalability and competitiveness.
By addressing these challenges and leveraging its inherent advantages, the pulp molding industry is poised for substantial growth as it meets the increasing global demand for sustainable solutions.
Conclusion
Pulp molding offers a transformative solution to global environmental challenges, combining sustainability, versatility, and cost-effectiveness. By leveraging renewable materials and eco-friendly processes, it addresses the growing demand for sustainable alternatives across industries. Despite challenges like energy consumption and labor reliance, continuous innovation and collaboration can propel the industry into a future of widespread adoption and market leadership.

Xiamen Bioleader Environmental Protection Technology Co., Ltd
Professional manufacturer of pulp molding eco-friendly biodegradable tableware and takeaway food packaging! Committed to disposable degradable eco-friendly tableware, we can provide customized pulp sugarcane pulp mold products for a wide range of customers. We have developed hundreds of different products for our customers: meal boxes, plates, bowls, bowl lids, cups, fruit trays, pizza boxes, dessert holders, seafood trays, industrial packaging products, and more. We can customize embossed logos for our guests and welcome contact for more details.